Products & SolutionsVOC Concentrator
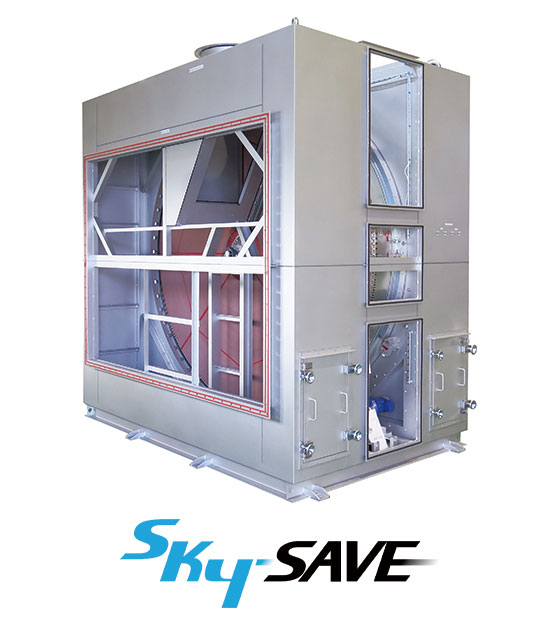
World-leading VOC Concentrator
We were the first company in the world to commercialize a rotor-type VOC concentrator model.We have a track record of delivering over 5,000 units in approximately 30 countries.
Product Lineup
Features
1. Maximum 30× concentration
2. Capable of removing 99 % of VOCs from exhaust gas
3. Silicon-free compatibility
4. High-boiling-point substance compatibility
What is VOC?
VOC stands for Volatile Organic Compound.
Examples : Toluene, Benzene, and Ethanol
VOCs are one of the air pollutants that generate suspended particulate matter (SPM), photochemical oxidants, and foul odors.
They are hazardous to human health, and many countries have established regulations concerning VOC emissions.
Sources of VOC exhaust gas
- Processes such as painting, printing, and coating
- Manufacturing facilities that use chemical substances or raw materials containing VOCs
Methods for treating VOC exhaust gas
The general method is combustion. Combustion methods are commonly used in industrial exhaust gas treatment, oxidizing the carbon in the VOCs into CO2. These methods can be classified into direct combustion, regenerative combustion, and catalytic combustion.
What is a VOC Concentrator?
A VOC concentrator is a system that concentrates VOC-containing exhaust gas.
Principles of VOC Concentrator

Benefits of Introducing a VOC Concentrator
- ■ Miniaturization of combustion equipment (reduced running and initial costs)
- ■ Annual reduction of CO2 emissions per combustion device
If the VOCs contained in the exhaust gas are low in concentration, combustion in a combustion device would require exceptionally large facilities and incur huge running costs. Therefore, it is possible to downsize the combustion equipment by concentrating the exhaust gas with a VOC concentrator. In addition, the high exhaust gas concentration also reduces running costs and decreases annual CO2 emissions.

VOC Concentrator Cassette

Components : Concentrator rotor, air seal, and drive part
VOC Concentrator Unit

Components: Concentrator rotor, air seal, drive part, plenum chamber, and duct port
Specifications
Model | Process gas volume※1 | Unit dimensions (mm) | Mass (kg) | Rotor drive※2
motor output (kW)
|
|||
---|---|---|---|---|---|---|---|
(Nm3/h) | (SCFM) | Depth A | Width B | Height H | |||
VMU- 965V40 | 6,400 | 4,100 | 1,200 | 1,940 | 1,275 | 700 | 0.1 |
VMU-1220V40 | 10,800 | 6,800 | 1,500 | 1,940 | 1,600 | 900 | 0.1 |
VMU-1525V40 | 17,000 | 10,800 | 1,750 | 1,940 | 1,850 | 1,250 | 0.1 |
VMU-1730V40 | 22,000 | 13,900 | 1,950 | 1,940 | 2,050 | 1,350 | 0.1 |
VMU-1940V40 | 27,500 | 17,400 | 2,150 | 1,940 | 2,250 | 1,750 | 0.1 |
VMU-2190V40 | 35,000 | 22,200 | 2,400 | 2,000 | 2,500 | 2,400 | 0.1 |
VMU-2450V40 | 44,000 | 27,900 | 2,700 | 2,000 | 2,825 | 2,900 | 0.2 |
VMU-2650V40 | 52,000 | 33,000 | 2,900 | 2,000 | 3,025 | 3,200 | 0.2 |
VMU-2950V40 | 65,000 | 41,200 | 3,250 | 2,000 | 3,375 | 3,800 | 0.2 |
VMU-3250V40 | 78,000 | 49,500 | 3,600 | 2,000 | 3,750 | 4,850 | 0.4 |
VMU-3550V40 | 94,000 | 59,600 | 3,950 | 2,000 | 4,100 | 5,300 | 0.4 |
VMU-3750V40 | 105,000 | 66,600 | 4,200 | 2,000 | 4,350 | 6,000 | 0.4 |
VMU-3950V40 | 117,000 | 74,200 | 4,400 | 2,000 | 4,550 | 6,350 | 0.4 |
VMU-4250V40 | 136,000 | 86,200 | 4,700 | 2,000 | 4,850 | 6,950 | 0.4 |
*1: For gas volume, the rotor surface wind speed is 3.0 Nm/s, and the zone division is 10:1:1. These are the values at 10x concentration.
*2: The motor is non-explosion proof. Explosion-proof versions can be supplied as options which are tailored to the standards of each country.
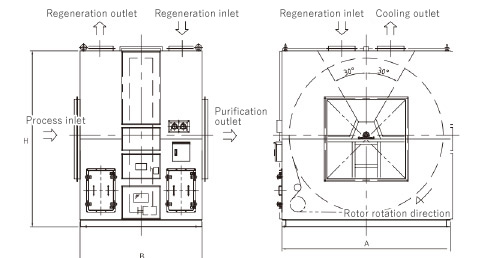
Options
We offer proposals that fit your usage conditions, so please consult us for details.
1. When silicone use is restricted
In applications like automotive painting or processes where catalysts are used afterward, there may be requirements for limiting silicone that can affect quality.
Z-Type : Zero-silicon specifications
Free of organic silicone and materials that affect paint quality. All components used have been evaluated and verified for integrity.
C-Type : Low-silicone specifications
Focusing on highly volatile organic silicon compounds found in silicone products.This type proposes a cost-effective solution by reducing these compounds.

2. If high-boiling-point VOCs are contained
If the treated air contains high-boiling-point VOCs, conventional regeneration temperatures may leave residues, causing deterioration of rotor performance. To prevent this, the K-Type (constant high-temperature treatment) and H-Type (periodic high-temperature treatment) are options for high-temperature regeneration treatment at 300 °C.
K-Type : Constant high-temperature regeneration
This is a solution for cases where high boiling point VOCs are the main component of the treated air.
H-Type : Periodic high-temperature regeneration
High-temperature activation treatment is performed periodically (usually once in every three months) to prevent the accumulation of high-boiling-point VOCs.

3. Clog-resistant rotor

In cases where the rotor becomes clogged due to paint or dust,
the clogging usually occurs within a range of about 10 mm from the end face.
R-Type : Replaceable end face section only
The rotor’s end face is manufactured with a split structure, allowing only the clogged 100 mm width of the end face to be replaced.
Furthermore, because it involves replacing divided blocks, heavy machinery is not needed for the replacement work, reducing costs significantly.

Application Examples
- Automotive painting
- Lithium-ion batteries
- Gravure printing
- Semiconductor manufacturing
- Ship painting
- Large-scale research facilities