Desiccant Dehumidifier – Purpose and Examples
The contents are excerpts from our track records. Please consult us for any concerns or requests.
Mold prevention | Moisture absorption | Rust prevention |
Condensation control | Early drying | Freezing |
Indoor low humidity | Production process air | For testing and experiments |
Purpose AMold prevention
Case A – 1
Dehumidifies outside air and supplies low-humidity air into the building.
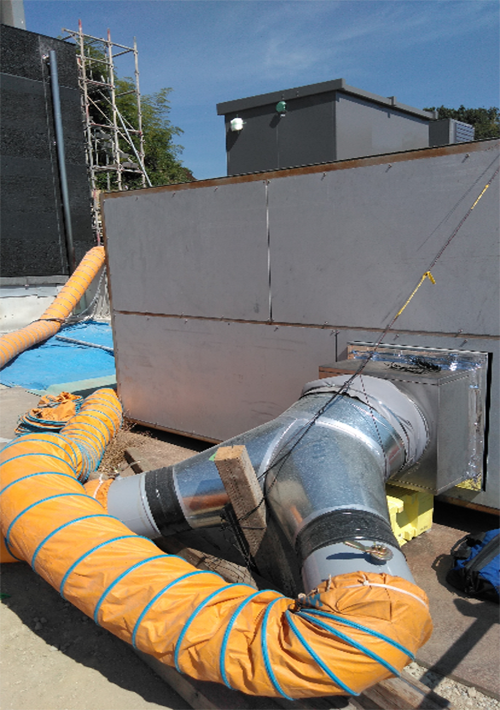
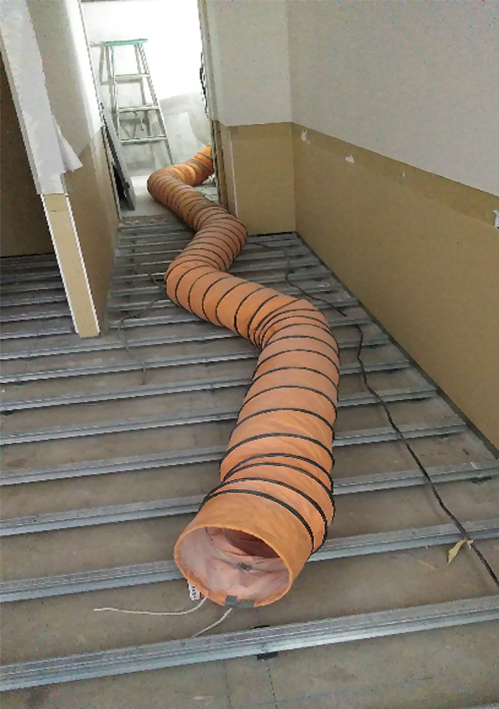
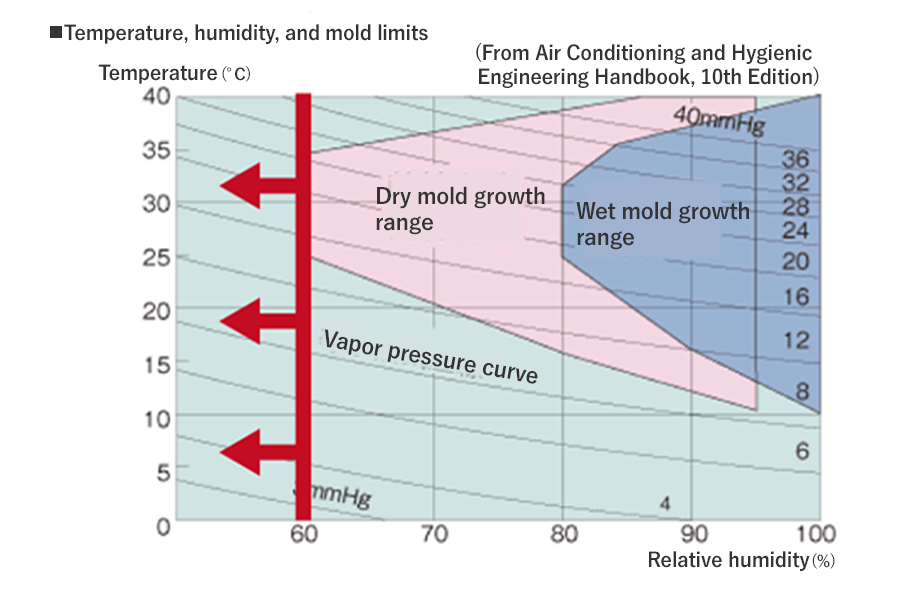
Before introduction
High humidity due to outdoor air intake.
(35 °C 80 %)
After introduction
Significantly reduced mold formation due to low humidity.
(50 °C 25 %)
Case A – 2
Low-humidity air supply to counter nighttime humidity increase.
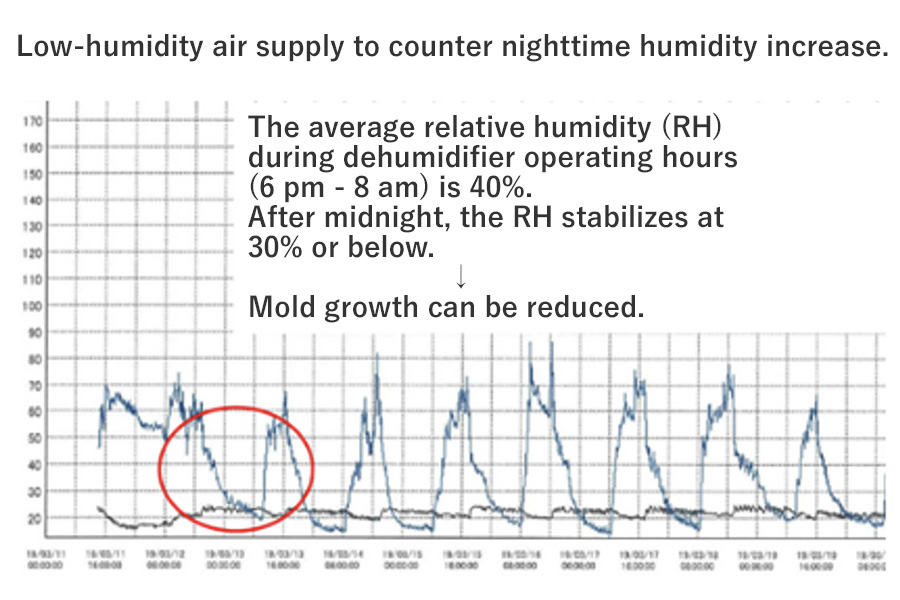
Before introduction
High humidity at night.
After introduction
Achieved low humidity by running the dehumidifier at night. Eliminate mold concerns and improve yield.
Purpose BMoisture absorption prevention
Case B – 1
Dehumidifies humid indoor air and supplies low-humidity air to the room.
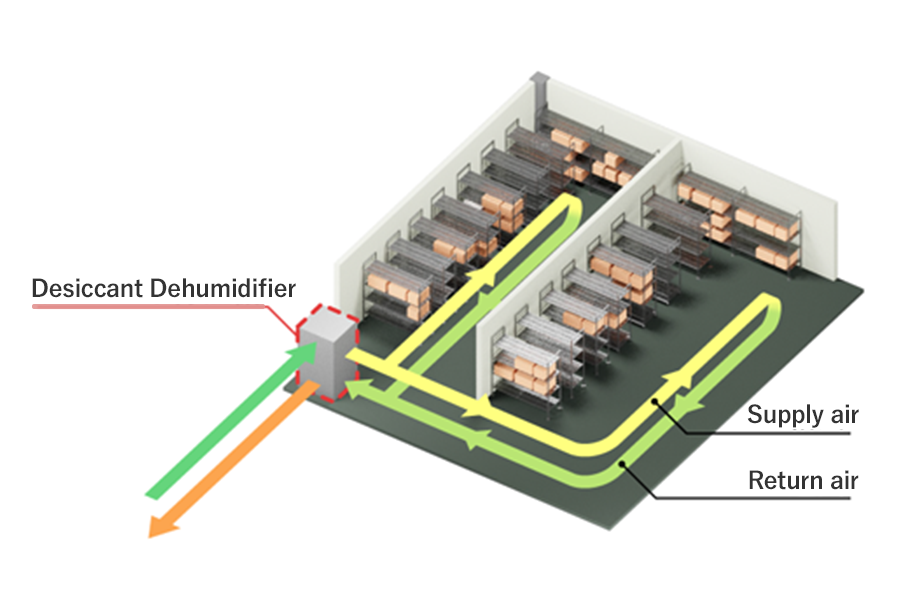
Before introduction
Powder solidification due to high humidity environment.
(Humidity 70-80 %)
After introduction
Prevention of solidification due to low humidity.
(Humidity about 10 %)
Case B – 2
Covering the production equipment with a booth and locally supplying low-humidity air.
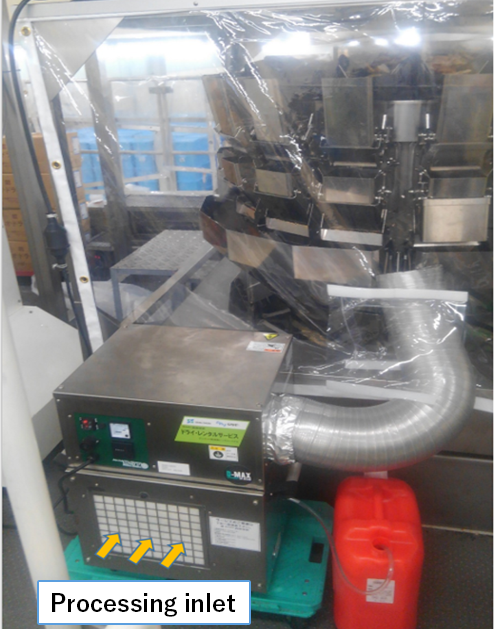
Before introduction
Clogging due to product moisture absorption and sticking.
(Humidity 70-80 %)
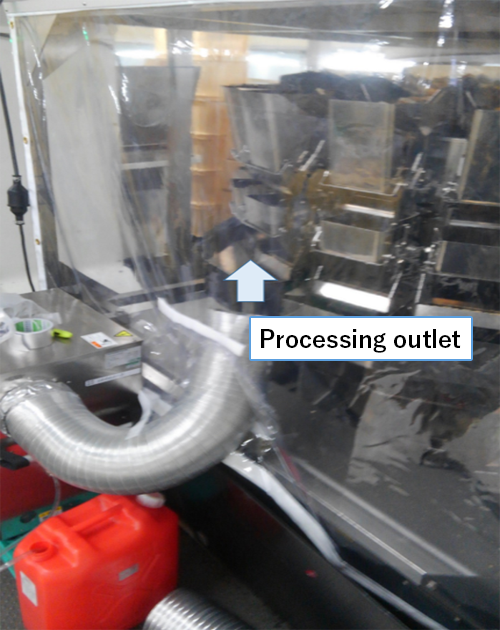
After introduction
Eliminates clogging due to reduced moisture absorption by dry air.
(Humidity about 10 %)
Purpose CEarly drying
Case C – 1
Provides low-humidity air to shorten drying time / prevent mold.
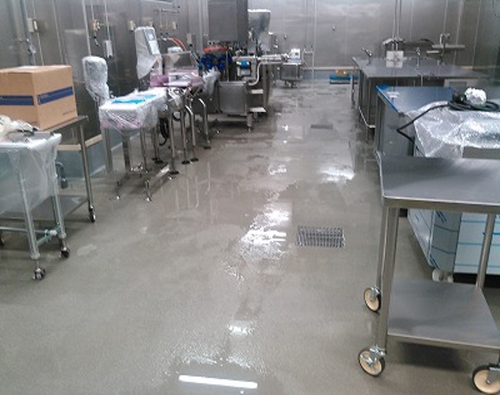
Before introduction
Introduction of outside air and natural drying.
Depending on the season, it may not dry even after 8 hours.
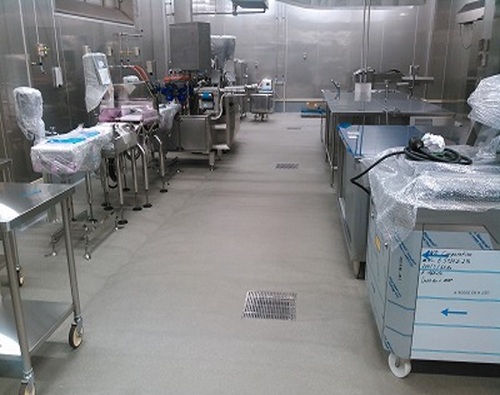
After introduction
Dry air introduction – Forced drying
Dries in 6 hours throughout the year.
Case C – 2
Provides low-humidity air to shorten drying time / improve productivity.
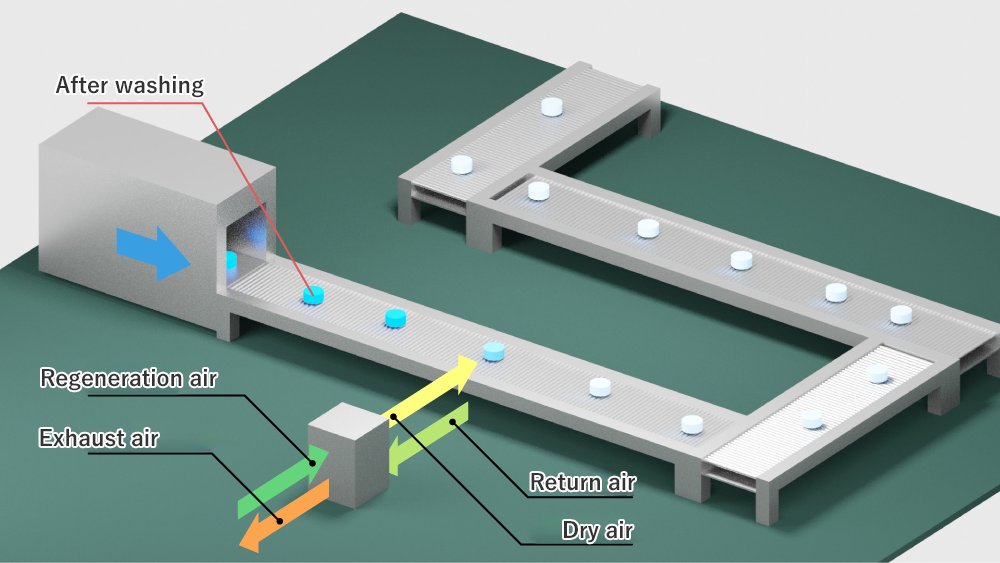
Before introduction
Outside air is introduced into the conveyor.
Drying time : 1,200 sec.
After introduction
Low-humidity air is introduced into the conveyor.
Drying time : 600 sec.
Purpose DCondensation control
Case D – 1
Supplies low-humidity air to prevent condensation on low-temperature wall surfaces in the room.
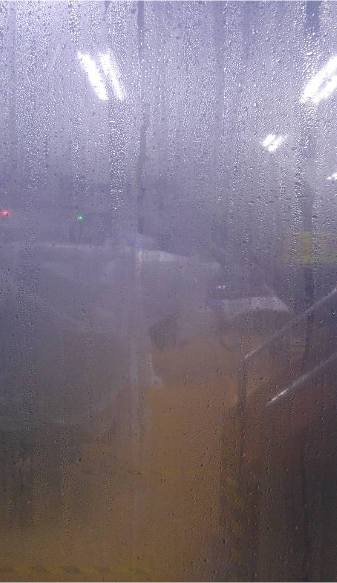
Before introduction
Indoor environment with condensation generation : 18.0 °C 100 %
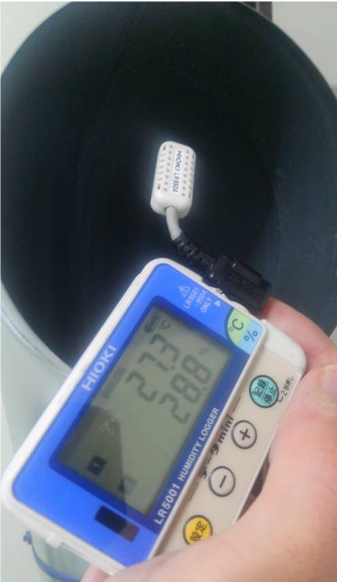
After introduction
Indoor environment : Achieved a significant reduction in humidity to 28.8 % at 27.3 °C. / Condensation was resolved, and mold floor slip concerns were eliminated to a large extent.
Case D – 2
Supplies low-humidity air to prevent condensation in low-temperature areas of ceilings.

Before introduction
Natural drying with a ceiling ventilation fan.
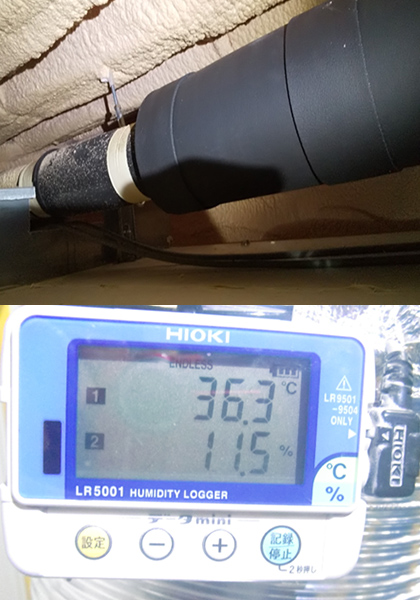
After introduction
Dehumidified air significantly improves condensation. Ceiling condensation leakage / mold was also improved at the same time.
Case D – 3
Supplying low-humidity air to the cargo handling room to prevent wall condensation at low temperatures.
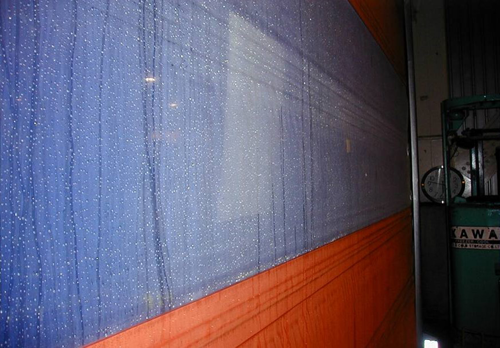
Before introduction
Low-temperature room : 15 °C 80 %
Cargo handling room : Condensation due to the introduction of outside air.
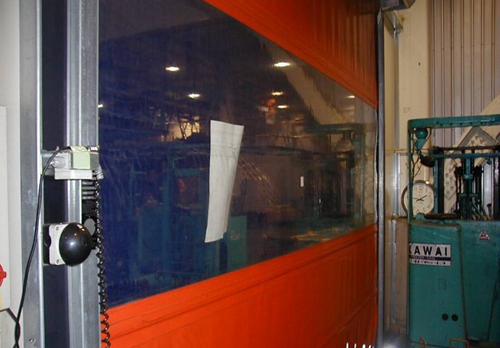
After introduction
Dehumidifies and improves indoor air to low dew point air. Improves issues related to wet floor and cardboard softening.
Case D – 4
Supplies low-humidity air to prevent the softening of corrugated board due to condensation.
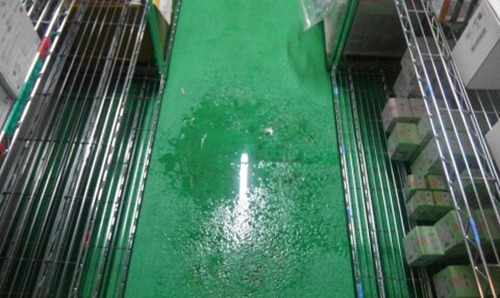
Before introduction
Condensation on the floor in a low-temperature room.
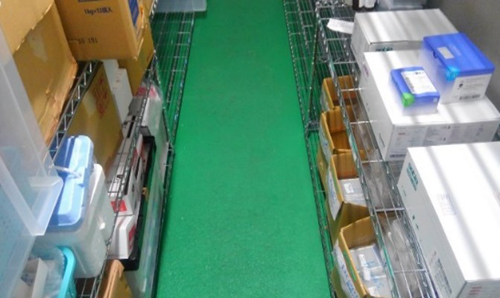
After introduction
Air quality improved to prevent condensation in low-temperature environments. Effective in preventing floor condensation and slipping.